Waterproof tanking techniques
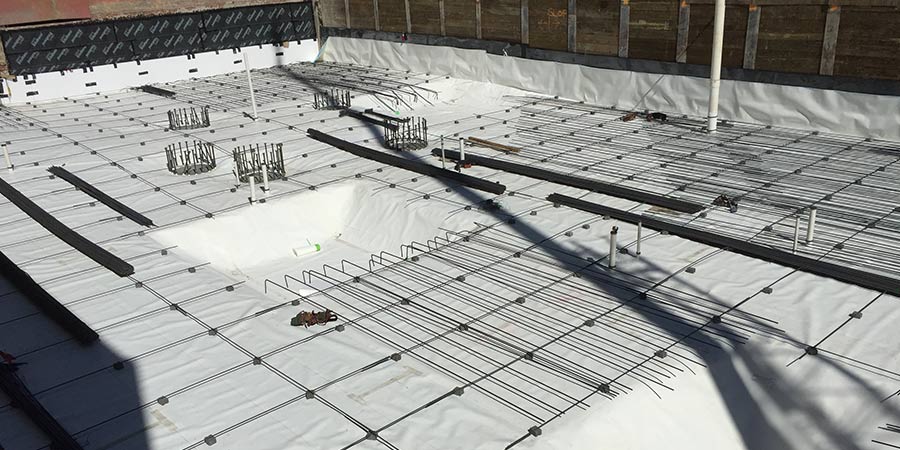
Tanking – also referred to as below ground waterproofing – involves the application of a waterproofing barrier to the walls, the base slab and in some cases to the roof of the below ground structure. The goal of waterproof tanking is to encase the entire envelope of the below ground structure to protect it from water ingress.
Tanking methods
The three types of waterproof tanking are:
- Waterproof concrete, where admixtures are added to the concrete to make it stronger and less permeable to water
- Drainage, or cavity wall construction, where water is allowed to enter the outer wall and then is pumped out
- Waterproof membranes, where there is a physical barrier placed outside of the below ground structure to keep moisture and gas vapour from entering the structure
The type of tanking specified depends on many factors, including:
- How the below ground space will be used?
- Will it be finished or unfinished space?
- Will there be valuables (ex, library books, medical equipment, luxury cars, household items, etc.) kept in the below ground space?
- What are the building owner’s expectations for performance?
- What is the budget for waterproofing?
- Are there resources to maintain the waterproofing system?
Waterproof concrete is often the least expensive option and is the easiest to deal with since there’s no separate application involved. Admixtures are simply incorporated into the concrete mix. There’s also little to no maintenance involved. Waterproof concrete is a good option for low- to medium-risk projects such as a concrete parking garage where having a small amount of moisture is acceptable. However, no concrete is 100% resistant to water infiltration so waterproof concrete alone is not the best choice for high risk projects or finished space.
Drainage systems can work well for situations when the use of an external waterproofing membrane is not practical or it is not possible to achieve continuity of an external membrane. Drainage systems do tend to be expensive, however, especially when you consider the cost of upkeep and maintenance. The systems need to be monitored to make sure they don’t get clogged. In addition, backup generators are needed in case of a failure.
There are also some buildings that use a drainage system to pump water out of the structure and use it as “grey water” (watering plants and similar purposes).
In general, drainage systems are not usually recommended for projects where there is a high water table, a fluctuating water table, or where there is contaminated soil, because allowing the water and/or vapours from contaminated soil into the structure is obviously not ideal.
Waterproofing membranes physically stop water from entering the structure. They are often used for high risk projects, such as luxury apartments or other finished space that would face significant issues if water, moisture, or vapors infiltrated the structure. Although it is acceptable to use drainage protection for critical basements, the risk of failure will be significantly reduced by using combined waterproofing protection such as using a drainage system in combination with a fully bonded waterproofing membrane.
The waterproofing membrane is applied prior to the pouring of the foundation. The concrete is then poured, creating a bond between the horizontal slab and the walls. Like waterproofing concrete, there is generally little upkeep needed once the basement waterproofing membrane is installed.
When choosing a waterproof membrane, it’s best to choose one that has an adhesive bond to the concrete, because this offers additional protection by enhancing the durability of the structure. In this instance, the basement waterproofing membrane is so bonded to the structure that the two become one entity, protecting the integrity of the structure itself and protecting the structure from water infiltration. Some membranes like PREPRUFE® Plus waterproofing membrane offer protection from water, aggressive soils, radon, and other hazardous gases such as methane.
Learn more about PREPRUFE® Plus waterproofing membrane
Tags
- Building Envelope Solutions
- PREPRUFE® PLUS
- Repair and Renovation
- Structural Solutions
- Waterproofing