Infrastructure projects
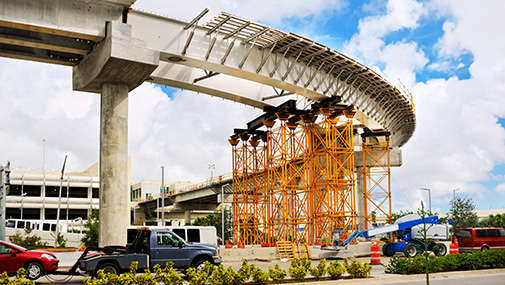
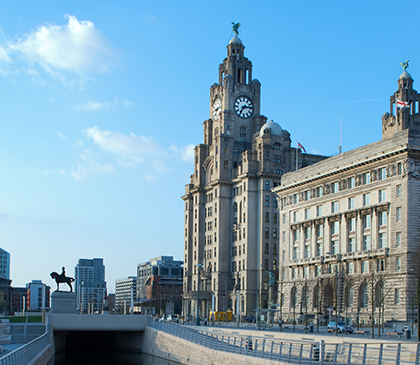
Transportation infrastructure along the banks of the Mersey River
Keep water in. Keep water out. Sometimes on a job, you need to do both.
That was true with the Liverpool Canal Link, a £22 million project that reconnected the Leeds & Liverpool Canal to Liverpool's South Docks. The construction included two new locks, two new bridges and three tunnels. The biggest issue? Keeping water within the canal while ensuring water couldn't penetrate the concrete tunnel.
The contractors chose our AT waterstop system, specifically developed for critical water-retaining and water-excluding structures. Both PROCOR® and SERVIBAND™ solutions were also used for waterproofing on the roof decks.
Since opening in 2009, the Canal Link has become a go-to destination in Liverpool.
Waterproofing the walkways at Expo Milano
Registered expositions (also known as universal expositions) bring in millions of visitors. The 2015 Expo was no exception. Over the course of 184 days, more than 20 million people visited the site, just outside of Milan, Italy.
All visitors had to walk across a set of bridges to get to the main Expo deck. That's a lot of foot traffic. Which is why during bridge construction, the contractors needed a high performance, waterproofing membrane. It had to offer resistance to hot asphalt. But it also had to provide complete adhesion and ease of application.
They chose our BITUTHENE® and SOLARSHIELD® solutions for the bridge deck areas. To ensure proper application, we also provided onsite support.
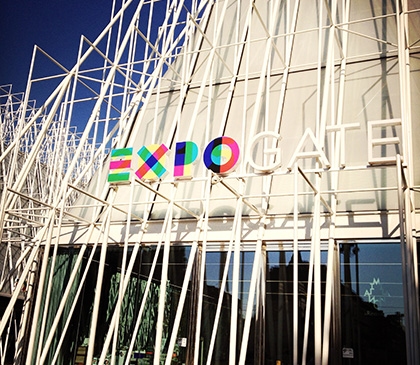
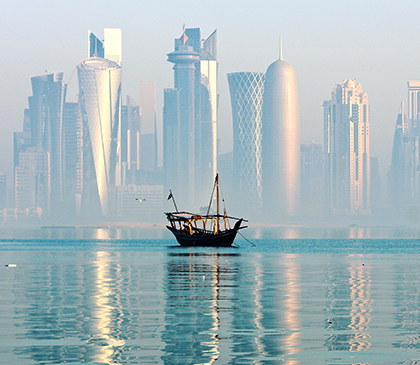
Raising a reservoir in Qatar
The Water Security Mega Reservoirs Project involves the construction of 64 concrete reservoirs. They will hold 27 million cubic metres of drinking water for the citizens of the Doha.
The specification called for extremely reliable concrete and waterproofing solutions. After all, the reservoirs will have to survive some of the harshest desert conditions in the world.
We identified a solution comprising DARAPEL®, ADVA XR® and PREPRUFE®. DARAPEL 75ME® is a high-performance waterproofing liquid admixture that reduces concrete permeability and shrinkage. ADVA® XR 3063D is a high-efficiency liquid superplasticiser.
The project began in September 2015 and is expected to use an estimated at 500,000m³ in concrete volumes.
Big bridges being built with precast
A bridge spanning the Fox River near Elgin, Illinois, needed to be rebuilt and widened from six to eight lanes, including full shoulders in both directions. Concern for structural integrity over the the lifetime of the bridge meant durability, corrosion control and high-strength were needed.
Using ADVA® Cast 575, specially formulated for the precast/prestressed concrete industry, provided excellent workability and slump retention for the creation of the massive structures required for the project.
The addition of DCI® corrosion inhibiting admixture was used to help maintain an active corrosion-controlling system within the concrete matrix throughout the lifetime of the structure.
The new bridge has eight spans supported by seven piers. The spans include 144 prestressed, precast concrete I-beams that are 150' to 170' long and 7'6" tall (around 45 to 51 metres long and around 2.25 metres tall). The bulb-T girders are massive, spanning from 150' to 168'6" (around 45 to 51 metres) and measuring 90 inches (228 cm) deep. The heaviest beams weigh an estimated 194,000 lbs. (87,997 kilos) and required special steerable trailers to transport.
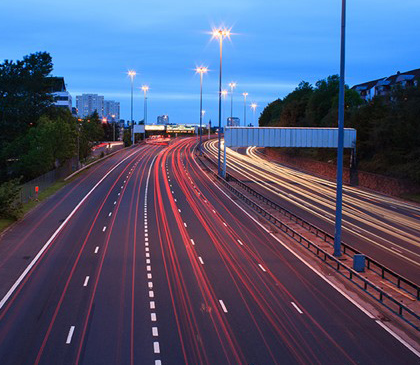
Major motorway repaired and protected for the long term
The heavily trafficked M8 motorway runs from Edinburgh to Dunblane, vehicles passing over joints in the road surface led to localized failure within the surface course. The fretted joints of the M8 needed repairing and sealing to prevent water ingress and further damage to the asphalt. The repair needed to be strong enough to cope with high volumes of traffic.
A rapid repair system was required to reduce disruption to road users during the maintenance project. Traditionally inlaid systems have been slow and consequently expensive to install, with unacceptable levels of traveller disruption.
The client selected the HAPAS-approved SAFETRACK® Inlaid Road Repair system. The system’s rapid cure meant that the road could be returned to full traffic load in as little as half an hour after installation. The system enabled more than 200 linear meters of fretted joint to be repaired per hour.
By using a highly durable crack sealing system, Transport Scotland has significantly increased the service life of the asphalt surface. Road user safety has also been improved by restoring the road surface to its original profile and reinstating its skid resistance.
Improving driver safety with high friction surfacing
The Trafford Centre is a large indoor shopping centre and leisure complex in Greater Manchester, UK. The SAFETRACK® HW high friction surfacing system has been in service there since 1998, enhancing driver safety on the roads and junctions leading up to Greater Manchester’s popular Trafford Centre.
The system was applied to more than 3,000m2 of deceleration and traffic signal areas near the heavily trafficked Junction 10 of the M60 Motorway. The system’s compatibility with the textured finish of the existing road surfaces, its speed and ease of application and the wide range of colours and aggregates available were instrumental features for the client. Application was undertaken during just two visits to the site.
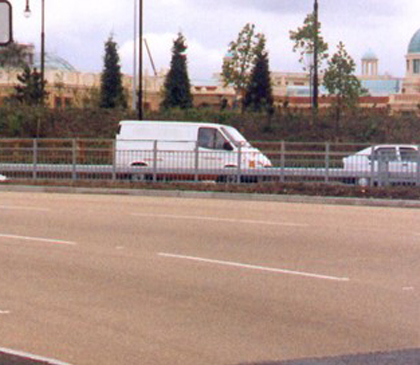
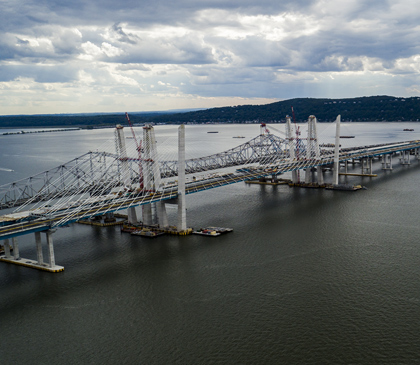
ELIMINATOR® bridge deck waterproofing system provides long-term protection for New York’s new Superstructure
The Tappan Zee Bridge, which opened in 1955 and crosses the Hudson River between Rockland and Westchester counties, has been replaced by The Governor Mario M. Cuomo Bridge, dubbed locally the “New Tappen Zee Bridge”.
The new bridge spans 3.1 miles across the Hudson River at one of its widest parts. Eight 419-foot towers, support the bridge’s cable-stayed main span. With its position battling the harsh winter conditions along the Hudson, the selected waterproofing system was needed specific sodium resistances from de-icing in freezing temperatures.
The ELIMINATOR® membrane’s proven track record of success on equally heavily trafficked new bridges along with the company’s 25 year record in the US meant that it ranked highly during the extensive review and analysis of bridge deck waterproofing systems carried out by the client.
With only two months to complete the application of the ELIMINATOR® system and an area of approximately 215,000sq ft. / 19974 m2 needing waterproofing per week collaboration with the specifiers from the early stages of the process guided a smooth and successful application with the team enlisted able to produce these challenging output levels to meet the project’s tight deadline.
World class combined waterproofing solution for Doha Metro Red Line South.
A new major metro system is under construction in Qatar’s capital city, Doha. The Red Line runs for 40 kilometres from Al Wakra in the south to Lusail in the north. With a total of 18 stations, the Red Line offers a convenient and reliable alternative to driving in the capital, cutting journey times from the airport to Lusail from an hour and a half drive to just 36 minutes on the metro.
Waterproofing protection is a vital aspect of the project. INTEGRITANK® and PREPRUFE® 300R Plus combined waterproofing system from GCP Applied Technologies, offered a world class solution for the Red Line South section of the project.
The works to be carried out were the waterproofing of five underground stations and five switchboxes on the Doha Metro Red Line South. This project required a fast track, durable waterproofing system that would withstand a predicted 120 years design life.
Having proved their compatibility and effectiveness on previous projects, the INTEGRITANK® liquid membrane and PREPRUFE® 300R Plus pre applied sheet membrane were selected to provide the waterproofing system of choice. PREPRUFE® 300R Plus composite HDPE adhesively sealed sheet membrane and INTEGRITANK® cold, spray applied liquid membrane combined to provide world class waterproofing.
The system demonstrated it met three key requirements: durable enough to last the design life of the structure, fast and simple application to expedite the construction programme, and the necessary protection from groundwater, sulphates, chloride and hydrocarbons.
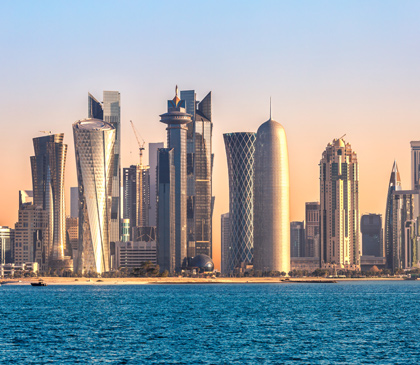
Liverpool Canal Dock Link is Successfully Waterproofed
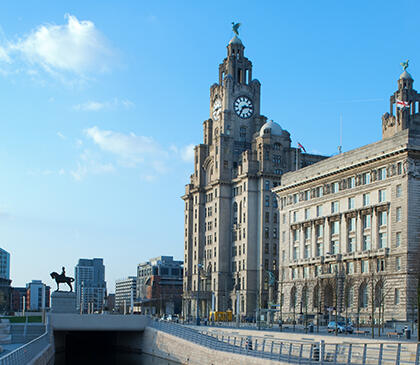