Specifying below ground waterproofing
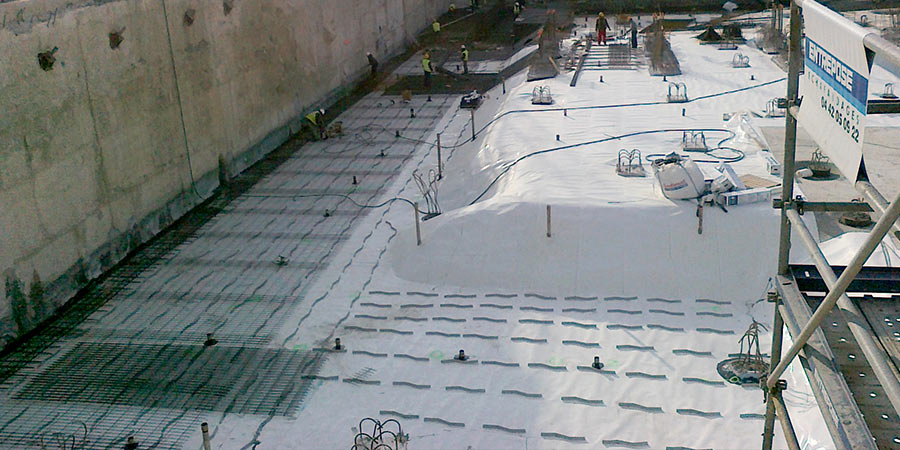
Waterproofing basements and other below ground spaces takes special considerations. Here are five points to consider when specifying waterproofing for these spaces.
Investigate the water table level and assess the risk of rising ground water levels due to high rainfall or flooding.
Unexpected rising ground water levels will increase the hydrostatic pressure on the waterproofing membrane, which may damage the membrane if the hydrostatic pressure exceeds the membrane’s strength limit. When the water table rises above the waterproofing membrane finish level, water will penetrate through un-protected area and cause damage to the structure.
On job sites involving either construction within the water table or where there is a risk of rising ground water level, it’s essential to specify high performance waterproofing to protect the structure.
Insist on zero lateral water migration.
Not all “fully bonded” membranes are the same. Be sure that your waterproofing membrane bonds adhesively to the structure. If the waterproofing membrane has a mechanical bond, any concrete cracking can easily result in water traveling between the structural concrete and the waterproofing membrane. When a leak occurs, often this is addressed with injection grouting, which is time consuming and expensive. Injection grouting is unlikely to fix the source of the problem because once you seal one leak, the water continues to migrate above the membrane to other cracks.
With a mechanical bond, typically the “bristles” of the membrane bond to the concrete but there are capillaries between the bristles where there is no adhesion between the concrete and the membrane. It is those spaces that leave room for lateral water migration.
Alternatively, with an adhesively bonded system, even if the membrane is accidentally punctured, any leaks would be restricted to that small area and would not migrate, since there’s no space between the concrete and the membrane for water to flow.
Specify a comprehensive system for floors and walls.
It’s tempting to want to forgo waterproofing on walls, but this should not be skipped, especially if the basement will be finished space. Water will always find the path of least resistance. Even miniscule cracks on a basement floor or wall can mean major costs to you and disruption for your building tenants. These water leaks beneath the surface can also lead to mold, which has the potential to cause significant health problems and potential liability issues.
Ask about manufacturer support.
Be sure your waterproofing will be applied by installers who are experienced in this work and trained by the manufacturer, and that the manufacturer will commit to preinstall meetings and site visits. There are many idiosyncrasies of each job site, so it’s important to have advice from manufacturing reps to ensure that the installer applies the materials properly in a way that meets the needs of that specific job site, and that all products being used are compatible with one another.
Get assurances about any contamination considerations (if the site is on reclaimed land).
If there is soil or water contamination at the job site, ask that the waterproofing manufacturer review your geotechnical report and ensure that their waterproofing membrane will not be adversely impacted by the contaminants onsite.
Learn more about below ground waterproofing.
Tags
- PREPRUFE®
- Waterproofing