Measuring ball mill ventilation
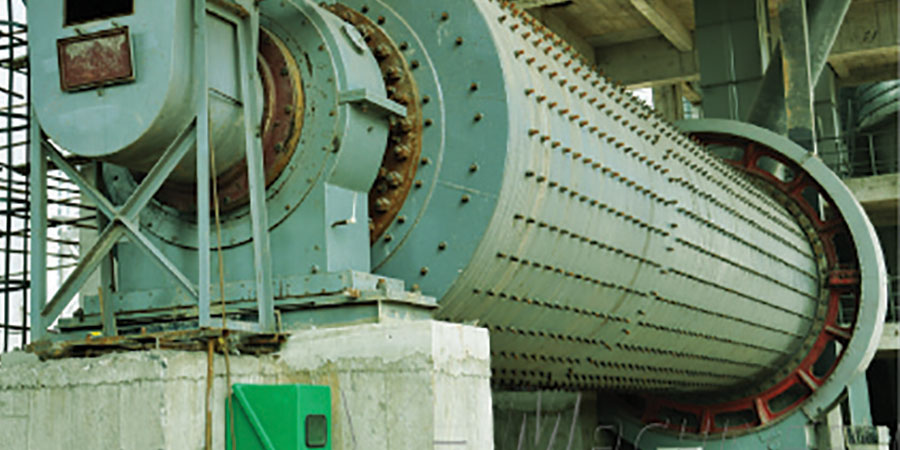
Mill ventilation is important for cooling the mill, removing moisture and improving mill efficiency. Typically, a velocity across the media of 1m/s is a good target. The challenge is to measure it.
Cement producers are required to measure and report to government agencies about the air that flows up the cement mill stack. The value of airflow in m3/hr can be back calculated using the mill diameter and media fill level to a velocity over the mill internals. However, the disadvantage of this method is that it also includes any false air that enters the mill system after the mill exit, through the mill seals, leaking sample points, air slides and the bag filter. If the mill is not well maintained, then this excess air can add up to quite a large amount.
It is preferable to measure the air velocity entering the mill inlet using a simple hand-held anemometer. This will indicate the actual air flowing into the mill and will discount the impact of false air. Some allowance does need to be made for any additional air that may enter either with the raw materials or back from the re-circulating load. Depending on the mill configuration, this can be anywhere from 25-100% additional air flow.
Experience has shown that an air velocity in the region of 7-10m/s at the inlet represents in the region of 0.8-1.0m/s through the mill.
In older mill systems, the mill inlet is often closed off, so it is not possible to measure the velocity directly. In these cases, you need to look for other clues. One simple test is to compare the mill outlet Blaine fineness with that of the mill filter dust. If the mill airflow is optimal, then the Blaine of the mill filter dust should be no more than 1000 Blaine greater than at the mill exit. If it is any finer, this indicates that the airflow is only sufficient to remove the lightest, finest particles from the mill and is therefore lower than optimum.
However, there is often no easy access to sample the mill filter dust. In such a case, one option is to take a sample from the base of the filter following a crash stop. In older mills, wear on the mill outlet seals can lead to a progressive and often unnoticed increase in false air, with a consequential reduction of actual ventilation through the mill.
Therefore, it is good practice to do this Blaine test on a monthly basis and ensure that there is a good mill filter exit sampling point.
A simple check for the degree of false air is to compare the mill cement exit temperature with the mill gas exit temperature. As the cement and gas leave through the mill exit at the same temperature in a well-sealed system, the difference in these two temperatures will be only a few degrees. If the temperature difference is in excess of 10°C, then this is an indication of excessive false air. Note: The gas temperature will never be higher than the cement temperature. If it is, then one of the probes is located incorrectly or is simply not working. In such a case, ask for a manual temperature check to be done in both locations.
Tags
- Cement production
- OPTEVA™