Making cement manufacturing more efficient
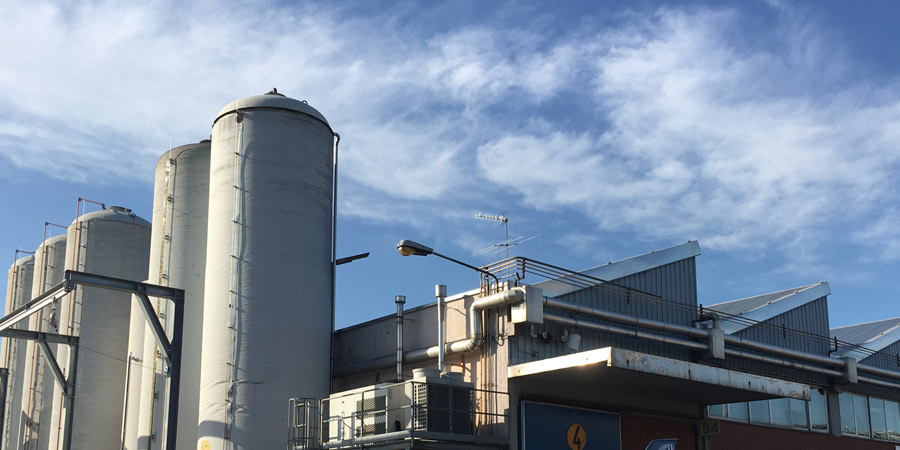
From concrete production to general contracting, there is a growing focus around the world about the need to reduce our carbon footprint. The increased awareness of CO2 emissions from cement production has brought focus on techniques that improve sustainability.
Grinding aids and quality improvers can reduce emissions
Two ways to reduce your carbon footprint is through grinding aids and quality improvers. Grinding aids reduce the energy needed for cement grinding, lowering costs and carbon emissions. This allows a 5% output increase (or 5% power savings) equal to between 1 and 3.5 kwn/ton of cement. Quality improvers increase strength, allowing the introduction of supplementary cementitious materials in place of clinker, reducing both costs and emissions.
Improved sustainability in cement plants
GCP helped a Tunesian cement plant use an OPTEVA™ CBA® quality improver to lower production costs, increase mill throughput, and reduce greenhouse gas emissions. The OPTEVA™ CBA® product enabled the plant to improve production by 20 tons per hour, or 17%. The plant reduced clinker factor by increasing limestone by 5%. The cement maintained comparable strength with lower production costs. With these measures, and production of one million tons of cement per year, the plant achieved 4,000 tons of CO2 reduction from electricity savings and an additional 45,000 tons of CO2 reduction from clinker replacement.
Grinding Aid only | OPTEVA™ CBA® | ||
Dosage | kg/t | 0.15 | 0.315 |
Mill output | Tph | 120 | 140 |
BSA | m2/kg | 317 | 308 |
Fineness, 90 mm | % | 9.5 | 8.5 |
SO3 | % | 2.1 | 2.1 |
Limestone | % | 11.9 | 17.0 |
Set time, initial | Min | 150 | 160 |
Set time, final | Min | 240 | 245 |
Strength, 2 day | MPa | 17.1 | 17.4 |
Strength, 28 day | MPa | 48.0 | 48.3 |
Another example is a cement plant operating in Algeria that produces more than five million tons of cement per year. The plant introduced GCP’s OPTEVA™ XS 255 quality improver, enabling an increase in limestone content from 6% to 15%, with a corresponding drop in clinker factor by 9%. This lowered production costs, and also reduced CO2 emissions by 365,000 tons per year. At the same time, both the strength and fineness of the cement increased, resulting in improved cement quality.
CO2 reduction could have been even greater, had the plant used increased grinding efficiency with OPTEVA™ XS 255 for improved throughput rather than increased fineness.
Untreated | OPTEVA™ XS 255 | ||
Dosage | kg/t | 1.2 | |
BSA | m2/kg | 340 | 388 |
Fineness, 90 mm | % | 4.2 | 2.8 |
CaCO3 | % | 6.1 | 15.2 |
Target limestone | % | 5 | 15 |
Air | % | 5.6 | 5.8 |
Strength, 2 day | MPa | 23.0 | 27.3 |
Strength, 28 day | MPa | 48.8 | 56.8 |
Normalized strength, 2 day* | MPa | 23.0 | 25.8 |
Normalized strength, 28 day* | MPa | 48.8 | 55.3 |
*Normalised fineness parameters of untreated cement
Discover more ways to improve sustainability.
Tags
- Building Envelope Solutions
- CBA
- Cement production
- Concrete
- OPTEVA™
- Structural Solutions
- Sustainability
- TAVERO™